Phenix City, AL – In July 2019, General Motors Co. made waves in the automotive industry with the release of the highly anticipated 2020 mid-engine Chevrolet Corvette Stingray. A dream more than 60 years in the making, the mid-engine Corvette features innovative components that maximize performance and blaze new trails for parts and processes within the automotive market.
One such part that GM highlighted during the July 18th debut is the automotive world’s first curved pultruded carbon fiber bumper beam. Produced by Shape Corp. with Vectorply Corporation carbon non-crimp fabrics, the multi-hollow bumper beam garnered national attention of its own within the composites industry. To date, the carbon bumper beam was nominated for the Society of Plastics Engineers (SPE) Automotive Process, Assembly and Enabling Technologies Award and been featured in numerous composite and automotive publications.
The first production model Corvettes will be available early 2020, but development for the crucially important carbon bumper beam began many years ago. In 2014, Vectorply joined forces with Shape Corp. to begin developing specialized carbon fabrics and laminate schedules for this vital part. Initially, Vectorply’s sales and engineering teams assisted Shape Plastic and Composites Engineering Manager Toby Jacobson with dialing in the ideal fabrics for the revolutionary curved pultrusion process. For this distinctive task, Jacobson, Shape’s team members and Vectorply’s staff turned to VectorLam, Vectorply’s proprietary laminate analysis software.
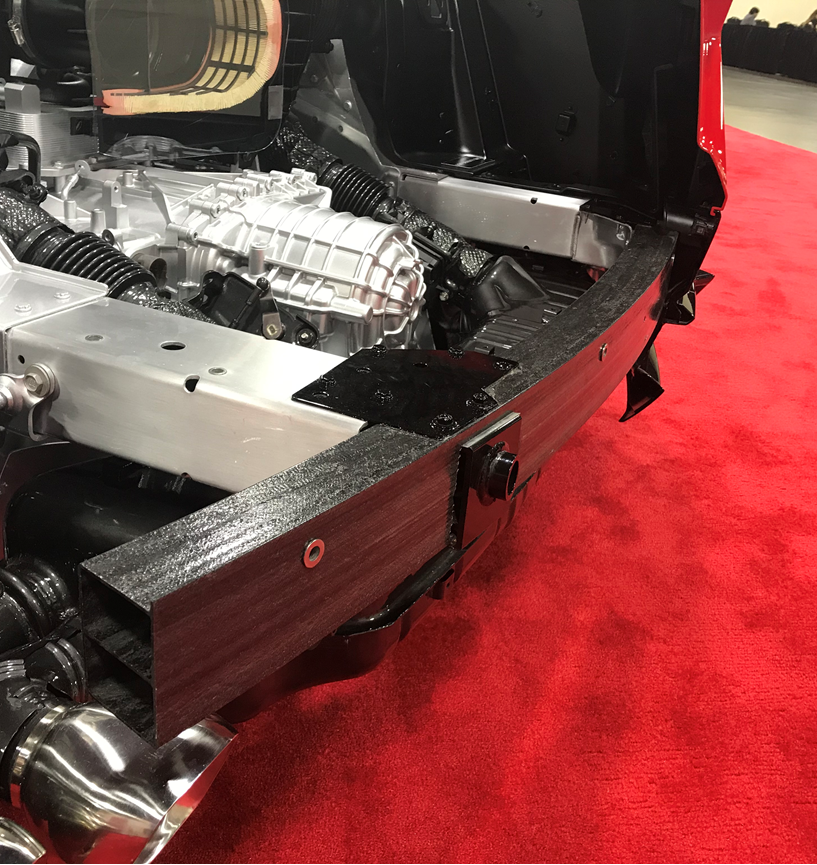
The 2020 Chevrolet Corvette Stingray features an industry-first curved, pultruded carbon fiber bumper beam produced by Shape Corp. with Vectorply carbon fabrics. Photo Credit: General Motors
VectorLam provides a cloud-based, multi-platform compatible approach to classical laminate theory and helps customers achieve goals of stiffness, strength, weight and cost by allowing users to design the perfect laminate for their application. Despite the wide range of applications VectorLam excels in, Shape’s industry-first part provided a unique challenge for Vectorply’s engineering team and software.
With adjustments to VectorLam required, Vectorply Senior Composite Engineer Molly Ditzler, P.E. accepted the challenge of tailoring the software to provide the perfect recommendations and data for Shape.
“We took the profile of their bumper beam and modified VectorLam to analyze their section so they could narrow in on the optimum laminate,” Ditzler said. “This was in the initial stages and Shape took it much further, including an FEA to verify the results.”
The hollow, curved bumper beam offered a unique challenge due to the complex structure dependent on multiple shear wall supports.
As the relationship between Shape and Vectorply grew, several different versions of advanced carbon fabrics were produced for testing and validation. According to Jacobson and Vectorply Northeast Region Sales Manager Seth Holman, this process helped both companies strengthen their expertise, processes, and quality.
“The support that Vectorply has provided has been unbelievable. I don’t think we’d be where we are now without them,” Jacobson said. “We asked Vectorply to do a lot of things that has been critical to producing the final design.”
Holman added that Shape’s requests helped Vectorply push their capabilities and production offerings to a new level.
“Through the entire development process, they have helped us think outside the box and be a better material supplier,” he said. “We’ve developed and maintained tighter tolerances in several key aspects that yield favorable processing and create efficiencies in Shape’s process. As time went on, they actually made us a better supplier and allowed us to prove our value in the process with our Production and Technical Services Team.”
In a high-end application such as the Corvette Stingray where each pound is key to performance, Vectorply’s wide range of carbon fabric production capabilities and technical assistance proved valuable to the success of the history-making bumper beam. As new markets and applications continue to push the boundaries of what is possible through composite production, Vectorply will play an integral role in the development and production of advanced composite fabrics to meet growing demands and expectations.
“Our goal at Vectorply is to help customers build the best products through the use of highly engineered composite reinforcement fabrics and optimized laminates, especially in new and emerging markets” said Vectorply President and Interim CEO Trevor Humphrey. “Shape Corp. and GM’s curved, pultruded bumper beam is a monumental accomplishment in the automotive and composite industries, and we are proud of the role that we played in the development and supply of specialty carbon fabrics for this groundbreaking application.”
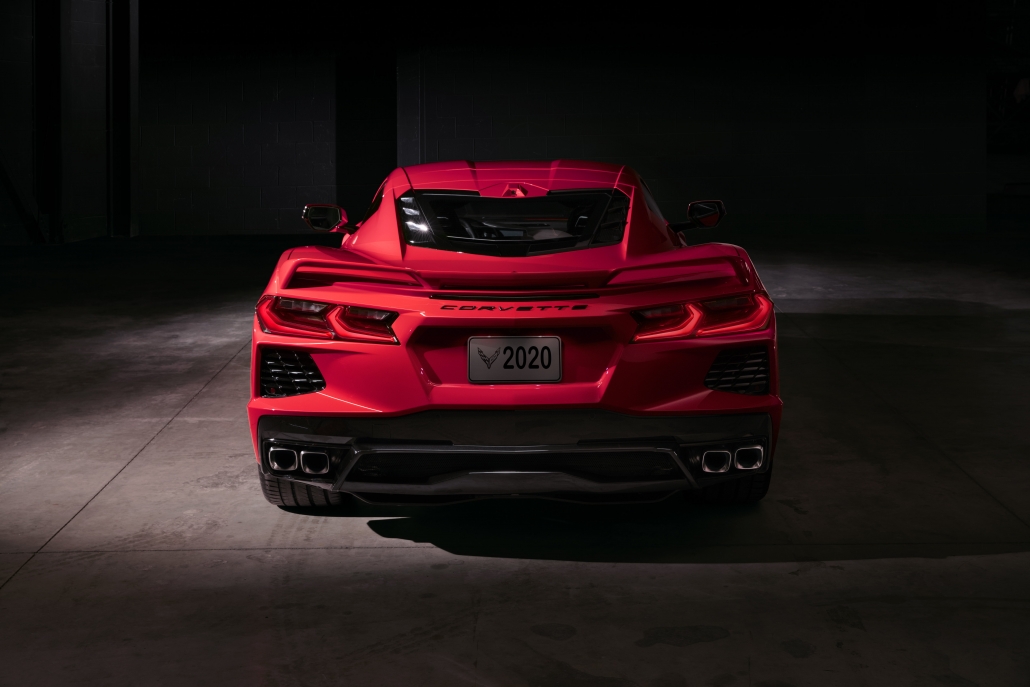
Photo Credit: General Motors